Choose the right Grinding Wheel – Grit Size
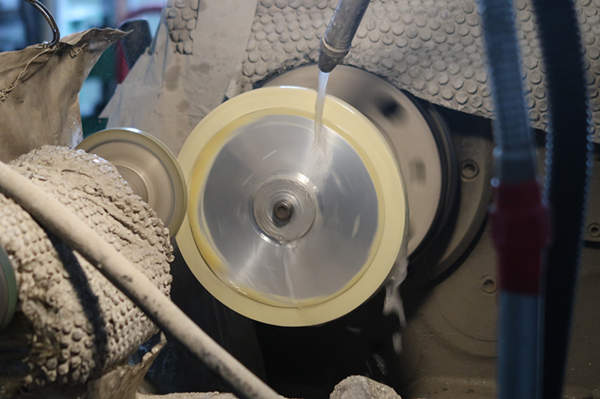
Choose the right Grinding Wheel
Grit Size
Size of abrasive grains found in a grinding wheel can range from 6 to 10, which is the coarsest, to even 1000, which is the finest. It matches the number of openings in the screen the grains pass through, e.g. the higher the number, the smaller the opening. Grain size influences stock removal rate, surface finish and wheel chip clearance – the larger the grain, the faster the cutting, but the poorer the surface finish. The finer the grain, the more suitable for fine, precision finish work.
For example, the coarse size is used when surface finish is not that important, like snagging operations in foundries and steel mills; the medium size is used when there’s a need to get a certain control over the surface finish, like high-stock removal operations; fine sizes grains are used for fine-finish and for operations that require small-diameter grinding; and extra-fine grit sizes are used for lapping and polishing operations.
Bond Strength & Wheel Structure
Wheels also differ based on the tightness of the bond that holds the abrasive and the grain spacing. The hardness or the grade of the bonding material ranges from A-H which would be classified as ‘soft’, I-P as ‘moderately hard’ to Q-Z which is ‘hard’. Wheel grade will determine the wheel speed, grinding depth, maximum and minimum feed rates, coolant flow, etc. Soft-bonded wheels are quick to release the grains, so the wheel wears out fast. When it comes to hard-bonded wheels, dull grains cause glazing, so the grains wear out fast, so the cutting edges are lost quickly.
As for the grain spacing, it ranges from 1, which would be the densest, to 17 which would be the least dense. Wheels with less grain density are open-structure wheels, they cut more freely, have a greater effect on the finish and can cut deeper and wider with less coolant.
Types of Bond
The wheels are also differentiated by the bond or the substance that holds the wheel together with varying degrees of strength. Hard-grade bond is a bond that spans between each abrasive grain and provides an extremely strong hold, while soft-grade bonds span little, so a small force is required to cause the release of the grains.
The bond influences the effectiveness of the cutting operation, and the type you will use depends on the wheel operating speed, the precision required, grinding material and the grinding operation. For example, the wheels with hard-grade bonds are used on high-power machines and jobs with small contact areas. Wheels with soft-grade bonds are used for fast stock removal, for hard materials and jobs with large contact areas.
Standard types of grinding wheel bonds are:
Vitrified (glass-based) – this type of bond is used most often – in 75% of all grinding wheels. The wheels with vitrified bond are rigid and strong even at elevated temperatures. Although they are unaffected by oils, acids and water, they have a rather poor shock resistance and can be broken down by the grinding pressure, which limits their application. They’re mostly used to 6,500 SFM;
Resinoid (resin-based) – this type holds the second place as far as the popularity goes and it’s the kind of a bond that softens under the grinding heat. The resin-based wheels are primarily used in rough cut-off, rapid stock removal operations, as well as those where better finishes are required – all at speeds up to 16,500 SFM;
Silicate (silicate-based) – silicate bonded abrasives are used when there must be minimal heat generated by grinding at a speed that is limited below 4,500 SFM.
Shellac (shellac-based) – wheels with shellac bond are not used for heavy-duty grinding, but for producing smooth finishes on parts like crankpins, rolls, camshafts and cutlery;
Rubber (natural or synthetic rubber-based) wheels are quite strong and therefore primarily used as thin cut-off wheels when burr and burn must be kept to a minimum, or driving wheels on centerless grinders, or to achieve extremely fine, smooth and high-quality finishes;
Metal (various alloys) – these are primarily used for bonding diamond abrasives, in operations such as electrolytic grinding.
Next bolg we will show you more about how to choose right grinding wheel , please keep following 🙂